Industrial Chillers: The Unsung Heroes of Modern Industry
Imagine a factory floor: towering machines whirring, sparks flying, molten metal glowing red-hot.
While the focus is often on the mighty equipment performing these tasks, a hidden hero lurks behind the scenes, ensuring everything runs smoothly – the industrial chiller.
Industrial chillers are the workhorses of temperature control. These sophisticated refrigeration systems act as the backbone of cooling operations in various industries, from manufacturing and pharmaceuticals to food and beverage production.
How Industrial Chillers Work
Industrial chillers function similarly to your home refrigerator, but on a much larger scale. Here’s a breakdown of the basic process:
- Heat Absorption: A designated fluid, often water mixed with glycol, absorbs heat from the process or equipment it’s meant to cool.
- Evaporation: This hot fluid enters the chiller’s evaporator, where a refrigerant absorbs the heat, causing it to transform from a liquid to a low-pressure gas.
- Compression: The refrigerant gas travels to the compressor, which significantly increases its pressure, raising its temperature.
- Condensation: The high-pressure, hot gas then enters the condenser. Here, either air (air-cooled chillers) or cooling tower water (water-cooled chillers) removes the heat from the refrigerant, causing it to condense back into a liquid state.
- Expansion: The cooled, high-pressure liquid refrigerant then passes through an expansion valve, which reduces its pressure and temperature further.
- Cooling Cycle Repeats: This cold liquid refrigerant re-enters the evaporator, ready to absorb more heat and repeat the cycle.
The cooled process fluid, meanwhile, exits the evaporator and circulates back to the equipment or process, maintaining the desired temperature.
Why are Industrial Chillers Crucial?
Industrial processes often generate significant heat. Uncontrolled temperatures can lead to a domino effect of problems:
- Reduced Equipment Efficiency: Overheating can cause machinery to malfunction, leading to production slowdowns and increased maintenance costs.
- Compromised Product Quality: Inaccurate temperature control can affect product quality, potentially leading to spoilage in food and beverage production or imperfections in plastic molding.
- Safety Hazards: Excessive heat can pose safety risks for workers and create fire hazards.
Industrial chillers prevent these issues by precisely regulating temperature. They ensure:
- Optimal Performance: Equipment operates efficiently, maximizing production output.
- Consistent Product Quality: Precise temperature control safeguards product integrity.
- Safe Work Environment: Maintains a comfortable and safe working environment for employees.
Different Types of Industrial Chillers
Industrial chillers come in various configurations to cater to diverse needs. Here are two main classifications:
- Air-Cooled vs. Water-Cooled: Air-cooled chillers use ambient air for condenser cooling, making them compact and suitable for smaller spaces. Water-cooled chillers rely on a separate cooling tower for condenser cooling, offering higher efficiency but requiring more space and a water source.
- Capacity: Chillers are sized based on their cooling capacity, measured in tons of refrigeration (TR). A 1 TR chiller removes the same amount of heat as melting 1 ton of ice in 24 hours.
Beyond Cooling: Additional Applications of Industrial Chillers
While their primary function is cooling, industrial chillers have broader applications:
- Comfort Cooling: They can maintain a comfortable temperature in large industrial buildings.
- Humidity Control: In certain processes, chillers can help regulate humidity by removing moisture from the air.
- Vacuum Systems: Chillers play a role in some industrial vacuum systems by helping to cool and condense vapors.
Choosing the Right Industrial Chiller
Selecting the right industrial chiller for your needs involves considering several factors:
- Cooling Capacity: The chiller’s capacity must match the required cooling load for your application.
- Temperature Requirements: Determine the temperature range needed for your process or equipment.
- Available Space: Consider the footprint and installation requirements of air-cooled vs. water-cooled models.
- Energy Efficiency: Look for chillers with high energy efficiency ratings to minimize operating costs.
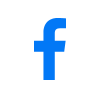
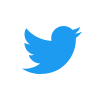
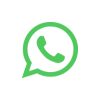
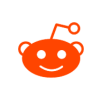
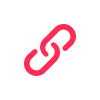
Recent Comments