The Humble Can Filling Machine: A Pillar of Modern Production
The ubiquitous aluminum can seems almost effortless to fill, yet the machinery behind this process is a marvel of engineering precision and efficiency. Can filling machines, crucial components of the food and beverage industry, operate tirelessly to deliver a constant stream of filled cans, ensuring a steady supply to consumers worldwide.
At its core, a can filling machine automates the process of precisely dispensing a specific amount of liquid product into a metal container. However, this seemingly simple task involves a complex interplay of various components working in harmony.
The Filling Journey: From Empty Can to Sealed Product
The journey of a can through a filling machine typically involves several key stages:
Infeed and Can Handling: Empty cans are loaded into the machine, usually via a hopper or conveyor belt. Sophisticated mechanisms ensure proper can orientation and positioning for filling.
Pre-Rinsing and Sanitization: In some cases, cans are pre-rinsed with water or sterilized to remove any contaminants before filling. This step helps maintain product quality and shelf life.
Filling: This is the heart of the operation. The filling valves dispense the product into the cans using various methods, depending on the product’s properties. Common filling techniques include gravity filling, volumetric filling, and pressure filling. For carbonated beverages, a CO2 purge may be performed before filling to remove oxygen and prevent spoilage.
Leveling and Sealing: After filling, the can level is checked for accuracy. Any overflow or underfill is rejected. Finally, the can is hermetically sealed using a seaming process to ensure product integrity and prevent leakage.
Can Ejection and Post-Filling Processes: Filled cans are ejected from the machine and may proceed to further processing like labeling, date coding, and packaging.
Types of Can Filling Machines:
Can filling machines come in various configurations to cater to diverse production needs. Here are some common types:
- Linear Fillers: These machines process cans in a single line and offer a more compact and economical solution for lower production volumes.
- Rotary Fillers: Ideal for high-speed production, rotary fillers utilize a carousel design, where multiple cans are filled simultaneously.
Beyond the Basics: Advanced Features
Modern can filling machines boast a range of advanced features to optimize production and product quality:
- Filling accuracy control systems ensure consistent fill levels, minimizing product waste and ensuring regulatory compliance.
- Automatic cleaning and sanitizing systems maintain hygiene and prevent product contamination.
- Data integration and monitoring systems allow for real-time production data collection and analysis, facilitating process optimization and quality control.
The Impact of Can Filling Machines
Can filling machines play a vital role in the modern food and beverage industry. Their efficient and automated operation allows for:
- Increased production speed and output: Meeting the ever-growing demand for canned products.
- Improved product quality and consistency: Ensuring consumer safety and satisfaction.
- Reduced production costs: Through efficient use of resources and minimized product waste.
The Future of Can Filling Technology
Continuous advancements are shaping the future of can filling machines. Areas of development include:
- Integration with smart factory systems: Enabling seamless data exchange and automated production control.
- Enhanced automation and robotics: Reducing human intervention for improved safety and efficiency.
- Sustainable design principles: Focusing on energy efficiency and minimizing environmental impact.
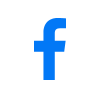
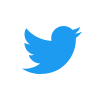
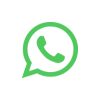
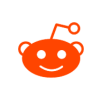
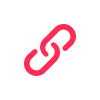
Recent Comments